Jone Gjerde can follow the production in Poland down to every detail, right from the comfort of his home. With 96 employees and up to 200 advanced Warehouse robots delivered every month, information is key.
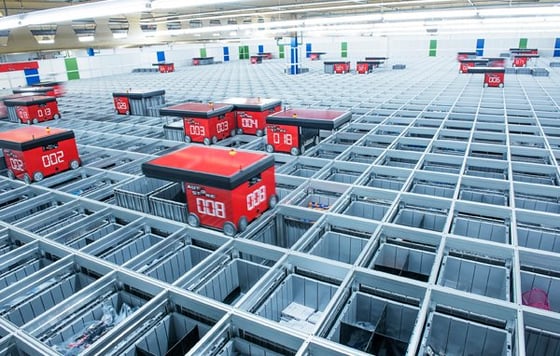
The Norwegian automated warehouse system AutoStore deliver warehouse systems to customers such as Puma, ASDA, Lufthansa, Komplett, and XXL. The robots are manufactured on a lean production facility in Poland, while development and sales are based in Norway. COO Jone Gjerde remains in control of all processes thanks to RamBase, an ERP-system developed especially for industrial and high-tech manufacturing.

– Our production is made-to-order. All sub-parts are ordered from external manufacturers and pieced together in our factory hall.
The manufacturing of advanced robots for an innovative new warehouse concept is complex. Control is essential throughout the production – you’ll have to maintain an efficient flow in the production process, while at the same time ensure high quality in all processes.
– The process starts with an order that needs to be registered in the system. This provides a list of which pieces are required, which pieces that need to be ordered, and when they need to arrive. The system also handles orders to our subcontractors – and everything happens automatically.
The system provides a full overview of all updates in sales, revenues, and costs, and all figures are easily available at all locations – both in the production facility in Poland and at our headquarters in Norway.”
Monitoring of service needs
When something is removed from stock, Gjerde will know it, and so will everyone else – immediately. The system provides everyone who needs the information and is authorized to receive the information, admission to all information simultaneously.
– If we alter something, for instance in the production drawings, everyone will be informed the moment it’s entered into the system. The cloud-based system ensures that everyone is updated – always. If you need to check something up against a drawing, it, and everything else you might need, is readily available in file locations that are accessible from anywhere – all you need is an internet connection.
And RamBase doesn’t let go of the robots even though they’re delivered to customers worldwide.
-Each robot has surveillance functionality installed. This reports errors on the robots directly to RamBase. This in return means that if a customer-owned robot at the customer’s facilities needs repairing, AutoStore will know this even before the customer herself is aware of this, and the AutoStore service team can be sent to the customer directly.
Control in a complex production process
The AutoStore robots are delivered to a growing industry. E-commerce, where all processes are automated, is increasing its market shares both in B2B and B2C trade. And even though it may seem obvious that the production process of the robots is also automated, this isn’t necessarily the truth. An automated process requires a system that is adapted to a complex industry, and this is where RamBase excels. RamBase has been built over the span of several years. It was first a built as Hatteland’s internal business system, but as the market grew, one saw that other businesses may struggle with the same challenges in traceability and quality as Hatteland did. RamBase was therefore introduced to the commercial market. It’s designed to handle and simplify the manufacturing process, the logistics process, and the interaction across country limits and currency zones. Finance is an integrated part of all operations, and provides real control in all business processes, throughout the value chain.
Considerable experience
Gjerde is responsible for the production in Poland and for the development in Norway, and his days are divided between the two countries.
-The system gives me the overview that I need. It’s by far the best system I’ve used in my 40 years of experience in industrial production.
COMMENTS