In early February, we attended the NFEA Smart Production event in Ålesund, an event that attracts professionals and enthusiasts from diverse organizations with a shared passion for learning and networking. This event opened the floor to industry leaders and businesses to showcase and discuss the critical role of sustainability within local production and manufacturing. The insights and reflections garnered from this two-day event are profound, and we are eager to share them with you, highlighting the significance and transformative potential of Norway's approach to smart production.
What is NFEA Smart Production?
The NFEA Smart Production event in Ålesund focuses on how digitalization and emerging technologies is driving profitable and sustainable production in Norway. This year's theme centered around The green shift and how manufacturing companies across the country are adapting to these changes.
Our Key Account Manager, Rune Løvdal was there and had this to say:
"The Smart Production Conference was a great experience for those of us who attended. The speakers delivered high-quality presentations that were both informative and entertaining. Many examples were provided on how automation and robotics, combined with a strong focus on sustainability and the green shift, make the Norwegian industry competitive."
Green industry focus
In recent years, the "green industry focus" has been on addressing visible polluters such as energy and transportation, but often overlooked the less conspicuous manufacturing sector. Industry is often out of sight, unlike the cars we drive or the electricity we use at home. Yet, it is here, in the heart of industry, where transformative change can have profound effects. Through two days of discussions, we've identified three distinct challenges that gave us food-for-thought and we want to share them with you.
Localization
In response to the fragility of global supply chains and a push for reshoring, a significant movement towards localized production is underway. This trend is prompting a strategic overhaul towards building regional production centers, reviving practices abandoned for offshore manufacturing decades ago. However, this resurgence of 'bringing production home' is not just a return to familiar grounds; it must be accompanied by a fresh wave of innovation and sustainable practices into the very fabric of manufacturing.
We attended a site visit to Spilka Industries, a company with a 90 years legacy in window hinge production. Recently, they have developed a completely new concept for exterior façade cladding for buildings. Their product, boasting a 60-year lifetime guarantee, weather resistance, and construction from 100% recyclable materials, sets a new standard in the industry.
But it's not just the product that sets Spilka apart; it's their manufacturing ethos. As we toured their facilities, we were impressed with their advanced robotic automation, which not only sets a benchmark in manufacturing efficiency but also aligns with sustainable practices. The market potential for such forward-looking ventures is significant, with Spilka's estimated market value in Norway alone reaching an impressive 15-16 billion NOK. The potential for international market expansion highlights the vast growth opportunities awaiting those who embrace this localized manufacturing model, pointing to a future where sustainability and innovation drive the global economy.
Flexibility
During the event, Norwegian shipping company, Ulstein, shared insights into their journey through energy and digital transitions, alongside their innovative strategies for sustainable marine operations. Drawing from their own shipbuilding heritage, Ulstein presented their strategy, moving from traditional shipbuilding to agile prototyping and flexible global manufacturing, they've overcome the limitations of a single shipyard model.
This approach has led to the development of four adaptable prototypes, catering to market demands, customer needs, and enabling construction worldwide. With their expertise and services, Ulstein can construct vessels anywhere in the world. Furthermore, their adoption of digital twin technology further demonstrates a commitment to operational excellence, enhancing capabilities and efficiency across the maritime sector.
Mobility
Additive production, also known as 3D printing, has revolutionized the precision and efficiency of many industries, and Norwegian company Effee group is doing some extraordinary things with this technology.
Effee Group's application of additive manufacturing enables the integration of temperature control mechanisms and the incorporation of robotics directly into the manufacturing process on offshore oil rigs. This facilitates onsite repairs with ease. Traditionally, the repair of tanks or pipes required items to be removed and shipped to an onshore facility. A process that not only incurred significant downtime but also halted production for an extended period of time.
This shift towards additive manufacturing introduces a new standard of flexibility and has become the norm in industries like floating production storage and offloading (FPSO) oil production, where on-site fixes are common. Beyond the operational benefits, additive manufacturing embodies an environmentally conscious approach by significantly reducing material wastage, aligning with a broader commitment to sustainability.
By migrating production processes offshore, corporations not only optimize operational efficiency but also unlock levels of flexibility. This model isn't merely about enhancing workflow; it's about sculpting a future where precision, sustainability, and ingenuity are working stronger together.
Securing your future success: How RamBase Cloud ERP elevates customer ambitions to new heights
It is amazing to learn how companies like Spilka Industries, Ulstein, and the Effee Group are adapting to the green shift. RamBase Cloud ERP has many customers who are embracing green technology or making sustainability part of their unique selling proposition. Ydra with their "Built to Last" philosophy is a great examples. You can read more about Ydra below.
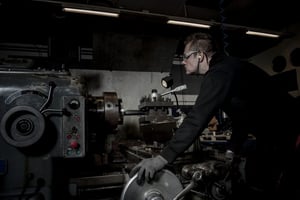