.png)
Quoting & Product Lifecycle Management
This is a pre-read for the "Product Lifecycle Management" session at the Summit 2024.
To get the most out of this parallel session we encourage you to read through and reflect how the questions and topics below impact your business, make sure to note down your talking points to bring to the Summit discussion.
We invite you to get inspired by solutions within the Configure Price Quote (CQP) and Product Lifecycle Management (PLM) space to improve the configuration and engineering support for designing and introducing new products.
What tools do you have to support your product engineering process?
Do you have some elements of engineering or configuration based on customer orders?
What’s your process for configuring, pricing and quoting products?
Do you spend too much time creating customer quotes and requesting quotations from suppliers on commodities?
Have you considered reducing the pain of lost orders by spend a minimal time providing accurate quotes using a CPQ system?
Do you design products and have a new product introduction process for your standard products?
Are your products complex and have several layers of approvals in the design process?
Your requirements might extend beyond the boundaries of the ERP system. Have you considered support from a PLM system in your product lifecycle management efforts?
Defining the required process support tools
Figure 1: Profit and loss trajectories throughout the product lifecycle
Traditionally, the product lifecycle is the cycle from the inception until the product is discontinued. From cradle to grave.
In the circular economy the lifecycle goes from cradle to cradle, from inception to re-inception. Although sustainability is an important topic in product lifecycle management, we will start off with the lifecycle phases development, introduction, growth, maturity, decline and disposal in this article.
This life cycle is particularly relevant for standardized products, where it applies for all products of the same product group and sold during the lifecycle. For low volume products, the lifecycle may differ and some of the phases become irrelevant.
The lifecycle will be limited to a unique end-product or a limited production series. The complexity of the product lifecycle vary across industries, as does the requirements to support the process of product lifecycle management. When developing standard products, the costs of development must be recovered over the lifecycle.
Figure 2: Committed versus incurred costs over product lifecycle
Most of the lifecycle costs of a product is committed during the development phase. Design decisions made during product development will impact the product’s ability to be profitable, as the incurred costs are predetermined at new product introduction. Attention to the component supplies and producibility is therefore of high importance during design. To manage this process PLM solutions are used.
- Tema for dagen
08.30 - 12.00
- Gjennomgang av sammenhengen i finansmodulen med resten av systemet.
- Kunnskap hva som skal være på plass for en periodeavslutning.
Lunch
UX Workshop
- UX gjengen fra produkt kjører en introduksjon til utvalgte RamBase prosjekter.
- God tid til inspill, ris, ros og spørsmål fra dere partnere.
PLM system basics
The processes related to the product life cycle comprise the following seven phases, which from a project perspective can be managed using a PLM system. However, other tools are required to work in harmony with a PLM tool or can other tools can to some extent have PLM features, making a separate PLM system redundant.
Figure 3: Product lifecycle management process
- Idea & Concept – Product Data Management (PDM) for documenting requirements and setting design conditions
- Design & development – PDM/ERP for specifications of functional and logical design, engineering drawings, bill of material, bill of processes, cost structures, quality approvals
- Prototype & pilot – ERP procure parts and produce first run, feedback to engineering on improvement on product design, material selection and process design, approvals
- Launch & ramp-up – ERP/PDM demand planning, ramp-up supplies and capacity, quality management for parts, processes and products in place
- Production and delivery – ERP/PDM source, make, sell and deliver
- Service & support – ERP/PDM/CRM service and support based on lifecycle information of installed base
- Phase-out and disposal – ERP/PDM phase out parts, end purchasing, reduce stock, recycle, reuse, dispose.
Manufacturing strategies and product lifecycle management
Process support requirements are dependent of product and industry specific manufacturing process strategies. The core of an ERP system will best support the processes of Made to Order (MTO), Assembly to Order (ATO) and Made to Stock (MTS).
There are different classes of Engineer to Order (ETO) strategies, related to if the process is project or product oriented. A project is from scratch typically with multiple disciplines delivering a complex product in a fixed position where the mix of disciplines and content might vary from order to order, or from project to project.
The process related to ETO products are product solutions within a predetermined range that needs to be engineered to fit the customer’s requirements. For both these variants, there might be standard parts, components or products that should be produced in a standardized way, but the final assembly is dependent on a set of disciplines working both in sequence and parallel.
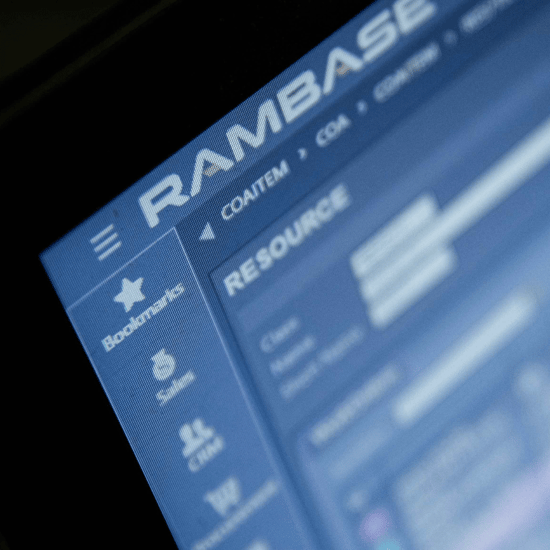
High engineering content per order
The left side of the illustration shows the product is customized with a high engineering content per order requiring project management for the engineering, final assembly or installation work. In contrast the products on the right side standardized and delivered repeatedly in a stock replenishment process.
It is a wide spectrum between these two opposite points. The need of a PLM system is limited when there is no lifecycle obligations for the manufacturer.
However, traceability related to product data, both as designed, and as built will be required by the customer that owns the requirements.
The lifecycle data is a part of the delivery. Product lifecycle management is related to the ownership of the product performance in the in-life part of the lifecycle. The producer in both ETO and MTO situations can have this responsibility and will need support in the complete product lifecycle management process. Some MTO producers are considered contract manufacturers, where the design is determined either as a separate process, or the design can be provided externally, typically by the customer. This will reduce the need to support a full product lifecycle process, but the customer is dependent of traceability data related to parts and the manufacturing process.
Product configurations
The middle part of the illustration is dedicated to product configurations, sometimes you will receive a product structure or part list from a customer, and you will need to turn around and see if the parts are available or will need some sort of revision based on availability or cost considerations. These are minor adjustments of components based on equivalent parts. You will need to keep track of the part list as it evolves before it is approved and ready to be put into production.
In the configure to order situation we can differentiate between the involvement of engineering to make configurational changes in the product structure (based on engineering knowledge), or if the changes are selections made by the customer while registering their sales order. This will typically follow a set of design rules in the sales configurator. A configuration might need to be manufactured based on the set configuration, or the configuration is related to the final assembly, then this variant of the product is assembled to order, here labelled ATO configure.
All the configuration methodologies relate to configuration of standard components. A product configurator can include the process for pricing, including price of parts, manufacturing and overhead needed to provide an accurate quote to the customer. To obtain an updated price and availability of components, a swift supplier quoting process might be needed. A CPQ system can have PLM features and a PLM system can have CPQ features. An ERP system can have both CPQ and PLM features, however, it is the required sophistication of the related processes that decides the tools your business will need.
All the manufacturing strategies related to standardized products will need to have a product development capability, usually supported by a PLM system to manage the product lifecycle processes for conceptualization, development, prototyping, launch, sustaining product during operations, and end of life.
Within that the capabilities of doing requirements engineering, component engineering, definition of bill of material, product variant and configuration management and handling engineering changes, and it might also include process engineering to create manufacturing bills of material.
A key indicator for the need of a PLM system is the number of new product introductions per year. With a high frequency, a specialized tool such as a PLM system might be required. Another indicator determining the product lifecycle process is the product and manufacturing process complexity, i.e. the number of levels in the structure, and operations per level.
Customized products
In an ETO scenario, the bill of material is not known at the point of contract initiation. There will typically be some engineering effort during the bid phase, to price the delivery as accurately as possible.
The parties agree on the requirements, a high-level design, a delivery date, payment plan, and a process for dealing with changes during the engineering, and production processes.
An ERP system will need parts and products to be defined to start planning procurement and production. When this information is transferred from the engineering system in the form of part definitions, engineering bills of material, and engineering drawings, the planning of procurement and production can start.
A quality plan and the routing of each production is defined during production planning, and the output is a manufacturing bill of material. The product lifecycle digital thread is all product related documentation that is aggregating throughout the lifecycle.
Some of the input in the digital thread is originated in the PLM system, as output from the different engineering stages, while other input originates from the ERP system.
Figure 5: Customized products
Click image to view full size
Deliveries from an ETO project installation might be documented through the PLM system, while ETO product deliveries might have the in-life servicing record in the ERP system. In any case the source of data should be considered with care when designing the processes determining the system requirements to support the business operations. ETO projects might not require process support for the service phase in the lifecycle, as maintenance might be subject to separate contracts being periodically renewed independent of the original contractor. In this process emphasis will be on getting a high-quality digital product lifecycle thread.
RamBase partner Mazeppa
Mazeppa er en av våre norske partnere som har solgt og supportert RamBase lengst i Norge.
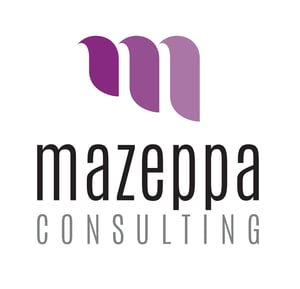
Smart Industri 2022
Mandag 23. mai kl. 09:00 – 17:00Tirsdag 24. mai kl. 09:00 – 18:00
Onsdag 25. mai kl. 09:00 – 15:00
Standardized Product
Take part in the discussion!
We hope you've noted down some ideas to bring to the session and trust that you now possess a thorough understanding of the various purchasing requirements processes.
Most importantly, we want to hear from you!
We encourage you to bring any questions or feedback to our workshop discussions, Your inputs will influence the direction of our development.