.png)
Plan and Promise
This is a pre-read for the "Plan and Promise" session at the Summit 2024.
Master the art of effective planning and learn to allocate materials and capacity strategically. From forecasting to order promising, we guide you in identifying the right tools, and leveraging RamBase's requirements planning features to fulfill promises confidently.
To get the most out of this parallel session we encourage you to read through and reflect how the questions and topics below impact your business. Make sure to note down your talking points to bring to the Summit discussion.

Reliable is being capable to deliver as promised.
How predictable is your fulfilment cycle?

Responsive is to have a high fulfilment rate and a short cycle time.
What delivery lead time does your market accept, and what do you do to compress the cycle time?

Resilient is to respond to variable needs and handling changes with low effort.
What is your balance between standardization and customizability?


Can you deliver what you promise?
Tailoring policies and tools to product strategies
What policies and tools should be used for your products’ different manufacturing strategies?
The planning process varies based on the specific context of your company, the marketplace, and your products. It is essential for the business performance to use the right tools for the job.
The manufacturing strategy for the specific product determines how order fulfilment and stock replenishment should be set up in the ERP system, which in turn determines the ability to plan the operations and promise deliveries.
Click here to view Process Diagram
The manufacturing strategy can be identified with the sales order decoupling point.
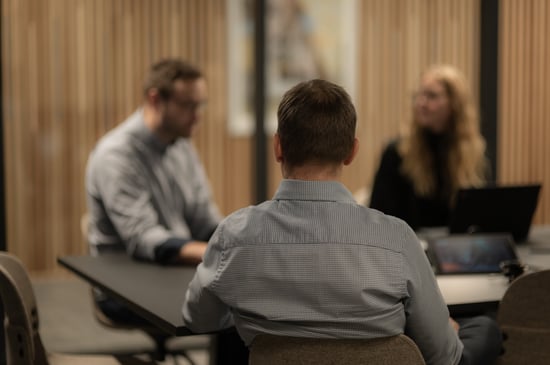
- Tema for dagen
08.30 - 12.00
- Gjennomgang av sammenhengen i finansmodulen med resten av systemet.
- Kunnskap hva som skal være på plass for en periodeavslutning.
Lunch
UX Workshop
- UX gjengen fra produkt kjører en introduksjon til utvalgte RamBase prosjekter.
- God tid til inspill, ris, ros og spørsmål fra dere partnere.

Let us dig a bit deeper to get into how different tools in RamBase can support these scenarios when it comes to planning and promising.
Make-to-Stock
Made-to-Stock (MTS) has a certain degree of predictability in demand and standardization of the products kept in stock. In the fulfilment cycle, the ability to deliver is determined by what is available in stock. This availability to promise is presented in the add product tab upon sales order item entry.
The replenishment of finished goods can be handled through different replenishment principles within inventory management.
Replenishment by dependent demand based on Materials Requirements Plan (MRP) is available through importing a Sales Forecast (FCC) or a master production schedule for the end items. This is a push system, in the sense that it pushes products that are planned into finished goods inventory.
The Sales and Operations Schedule (SOP) application in RamBase will guide you through producing a modified master production schedule, generating the manufacturing requirements and a procurement plan. Use this feature to create production work orders for the end items for an appropriate time horizon and create purchase orders for long lead items. The calculations in SOP does not consider allocations according to the Stock Assignment Register (SAR).
As orders on end item is created, the production and procurement requirements are cascaded and allocated through material requirement calculations.
Ongoing production is managed through the Production Work Order Menu (PWOMENU) and in the Procurement Requirements Application (PUR). By using this method, the direct relations between end item plan, productions, and procurement is kept intact for full traceability.
Replenishment of MTS products can also be managed in a pull system, by creating a demand driven MRP process for continuous or batch replenishment. Calculate and set reorder point and batch size or minimum stock level on stocked end items. When reorder point is used without an order quantity, it functions as an order up to level. When you check the requirement, the quantity that is below the reorder point will be set as order quantity. You can use Requirements Overview (REO) periodically to create end item production orders. Cascading requirements handled in production planning and procurement requirements applications.
Assemble-to-order
Assemble-to-order (ATO) promising is dependent on the capacity on the final assembly line, as well as the availability of sub-assemblies and other components. This can be investigated through the Lead Time Calculator (LTC) during order entry.
Final assembly is produced based on end item sales orders and delivered according to estimated delivery date.
Click here to view the Process Diagram
The replenishment side of the decoupling point can be set up as for make-to-stock, based on end item forecasts. Instead of creating production work orders on the end item, it is the stocked semi-finished products that are subject for make-to-stock.
Procured components in the final assembly should be kept in stock as well. These can be purchased based on using the SOP or REO application. Make dedicated purchase groups for singling out these parts.
.jpg?width=950&height=634&name=aksdal_STOCKS_2022_WEB%20(35%20of%2070).jpg)
Make-to-order
Made-to-Order (MTO) manufacturing might be buy-to-order for some categories of raw material. The fulfilment cycle is a bit more complex, as there might be more uncertainties related to promising a delivery.
Promising is dependent on internal manufacturing capabilities, availability of components in stock, as well as suppliers’ ability to fulfil their orders. The nature of customization will require that most of the requirements are directly generated by the sales order and keeping this dependency is crucial for effective fulfilment.
Click here for the Process Diagram for replenishment based on sales orders
If the MTO product lends itself to some degree of standardization in terms of supplies, the order-based manufacturing process can be combined with inventory management based on reorder point and batch sizes.
For all methods that rely on reorder points using stock level to manage the inventory, there should be calculated values to be entered into the respective fields in the system. If the part is strictly controlled by MRP, the fields for reorder point, reorder quantity should be blank.
Click here for Process Diagram for replenishment based on reorder polices
RamBase partner Mazeppa
Mazeppa er en av våre norske partnere som har solgt og supportert RamBase lengst i Norge.
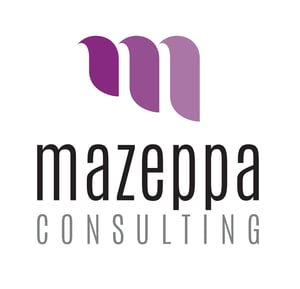
Smart Industri 2022
Mandag 23. mai kl. 09:00 – 17:00Tirsdag 24. mai kl. 09:00 – 18:00
Onsdag 25. mai kl. 09:00 – 15:00
Take part in the discussion!
We trust that you now possess a thorough understanding of the various manufacturing strategies.
Most importantly, we want to hear from you!
We encourage you to bring any questions or feedback to our workshop discussions. Your inputs will influence the direction of our development.